When building and operating a cleanroom, proper care must be taken to minimize contamination. This is because the tiniest of particles can cause significant damage to sensitive products or substances manufactured in these controlled environments. However, there are several risks associated with operating a cleanroom that stakeholders must carefully consider.
Contamination from Operators
One of the most significant risks associated with cleanrooms is the potential for contamination from the operators inside the rooms. Even with proper training, operators can unknowingly contaminate the products or substances they come in contact with, creating significant problems down the line. To mitigate this risk, employers must provide appropriate personal protective equipment (PPE) that includes cleanroom suits, full-body suits, gloves, and face masks.
Equipment Failure
Another significant risk associated with cleanrooms is that of equipment failure. Unmaintained or malfunctioning equipment can generate particles that counteract the cleanroom’s purpose and significantly damage the products being produced. Employers must ensure that all equipment used in the cleanroom is appropriately maintained and failsafe.
Human Error
The presence of human beings inside the cleanroom comes with its own risk of human error, which can cause considerable damage to the products or substances being produced. The most common form of human error in cleanrooms is failing to follow proper procedures. To reduce this risk, cleanroom operators must be well-trained on the procedures and understand the consequences of deviating from them.
Product Contamination
Products can also pose a threat in cleanrooms. When products enter the environment, they may carry microscopic particles that contaminate the entire environment, which can cause a significant problem. Employers must ensure that all products entering the cleanroom have been adequately sterilized and will not contaminate the environment.
Static Electricity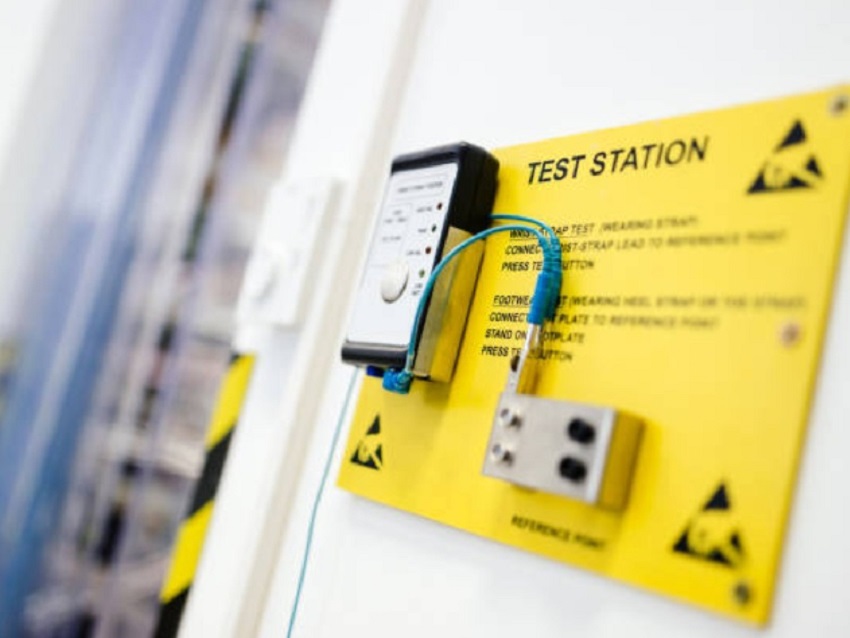
Static electricity is another risk associated with cleanrooms. When operators or equipment within the cleanroom generate static electricity, they can attract unwanted particles, leading to contamination. Employers must take appropriate measures to minimize the static electricity generated within the cleanroom to reduce this risk.
Conclusion
In conclusion, operating a cleanroom comes with its own set of risks, the most significant being contamination from operators, equipment failure, human error, product contamination, and static electricity. Stakeholders must consider and mitigate these risks to ensure that the products being produced in these environments are of the highest quality and meet the required standards.
FAQs
- What is a cleanroom?
A cleanroom is an environment that is free of pollutants for manufacturing processes or scientific research. - Why are cleanrooms essential for manufacturing products?
Cleanrooms are essential for manufacturing products because they help to reduce the risk of contamination, leading to high-quality products. - What is PPE, and why is it necessary in cleanrooms?
PPE stands for Personal Protective Equipment, and it is necessary in cleanrooms to protect operators from contaminants and prevent the contaminants from entering the cleanroom. - How often should cleanroom equipment be maintained?
Cleanroom equipment should be adequately maintained according to the manufacturer’s instructions and an appropriate schedule to minimize the risk of malfunction. - What is static electricity, and why is it dangerous in cleanrooms?
Static electricity is a buildup of electric charge on an object’s surface. In cleanrooms, it can attract unwanted particles and cause contamination, which can be dangerous for the products produced in these environments.